Non-Metallic Engineering Materials - Designing with Tufnol Laminates
Tufnol laminates are non-metallic engineering materials made from layers of fibrous reinforcement, such as cotton cloth, paper or woven glass cloth, which are bonded together with high quality thermosetting resins. In manufacture, the paper or fabric is first impregnated with the resin. Then, layers of this impregnated material are pressed together under high pressure and heated to about 160oC. This causes chemical changes in the resin, making it harden, and fusing the laminate into a tough, strong solid. By using alternative resins with different types of reinforcements and additives, a range of grades is created, with types to suit a wide variety of applications.
Also, by rolling or shaping the impregnated layers before pressing, stock shapes such as rods and tubes can be moulded. The resulting Tufnol laminates combine mechanical strength with excellent chemical and weather resistance.
They are rigid, with high strength and low weight and some grades can be used in temperatures ranging from around absolute zero to over 250ºC. They are also extremely useful for electrical and thermal insulation.
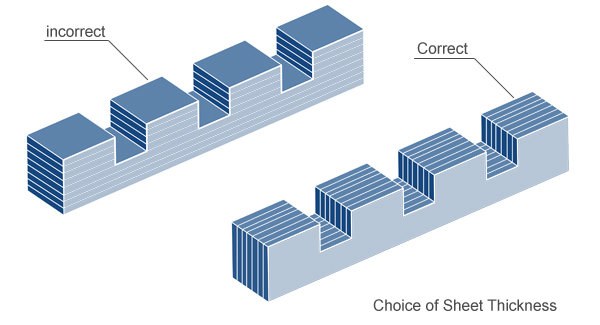
The designer who is considering using a laminate for a particular application should always bear in mind the fact that the material has a laminar structure and therefore has different strengths in different directions relative to the layers. It is therefore essential to ensure that the correct section of material is chosen, so that the laminations lie in the best direction to deal with the stresses involved.
Even where components are not required to withstand any load in use, machining to produce the component itself causes stress. Lack of consideration for the structure of the laminate can lead to fracture during production, handling or transit.
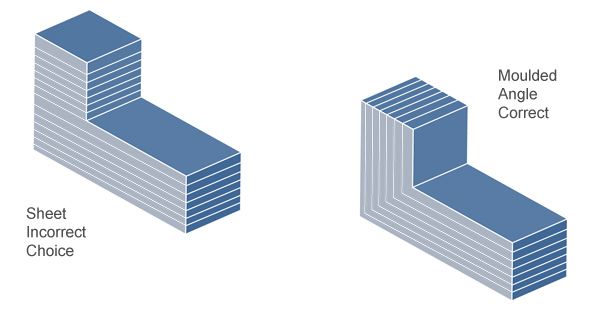
This image illustrates several examples where the laminar construction has influenced the choice of section away from the most immediately obvious.
Many laminates are slightly sensitive to stress concentration and, as with other materials, wherever possible it is good design practice to avoid stress-raising features, such as sharp internal corners or sudden changes in section.
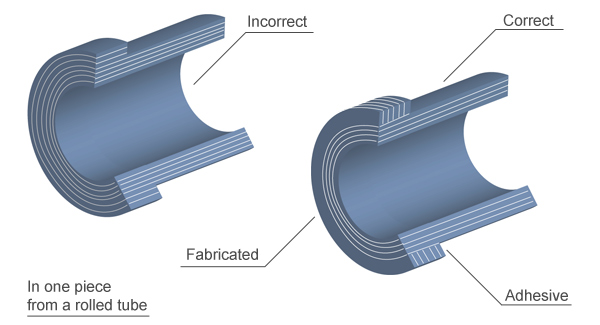
High-pressure laminates cannot be moulded to precisely accurate dimensions and, when selecting sizes of standard materials for ordering purposes, an allowance should be made for the possible variations in, for example, the moulded thickness of a sheet or the concentricity of a rolled tube.
These are usually greater with the coarser reinforcing materials and reference should be made to the British Standard relevant to the particular type of laminate.
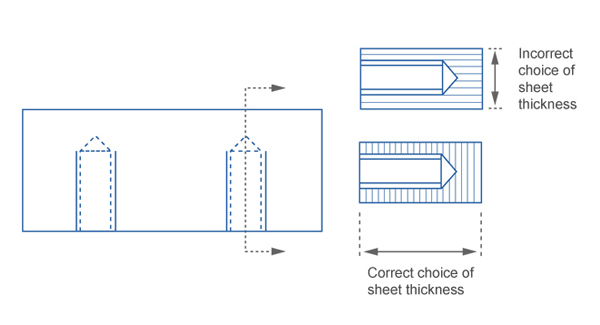
Owing to the nature of the material, components cannot normally be machined to the finest tolerances achievable with metals; however, the surface of a laminated plastics component has a slight resilience, which usually renders very fine tolerances unnecessary for good fits to be achieved.
Laminated bushes require a greater interference than metal bushes so that the same machining tolerance becomes much less significant. On the other hand, when inserted, the laminated bush may compress slightly on the bore, so an allowance may have to be made for this when determining the size to be machined. Similarly, the fibrous nature of the reinforcement causes considerable difficulty in achieving fine surface finish readings on machined faces.
This obviously varies with different grades but, for example, a first-class milled face on a medium weave fabric laminate may record a surface finish of 3 to 4 micrometers (125 to 160 micro inches) and even prolonged polishing may only reduce these figures by half. Once again, the resilient surface of the laminate usually makes fine finishes unnecessary. The milled face mentioned above would be entirely suitable as a bearing surface, without polishing